Factory equipmentIntroduction of the machine
Tanda Factory
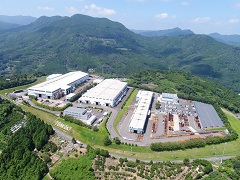
Site area: 116,678 ㎡
(1.65 times the size of the Fukuoka PayPay Dome)
In March 2005, the Tanda Factory completed conversion to an integrated production system that enabled it to produce large cylinders from materials until finished product. The foundry also improved its “clean foundry” capabilities in order to further improve the strength and quality of materials. The machine shop is using its high-precision machine tools and the processing skills it has developed over the years to improve its processing accuracy and reduce lead time through a more efficient production workflow as part of its efforts to improve its craftsmanship in order to better satisfy customers.
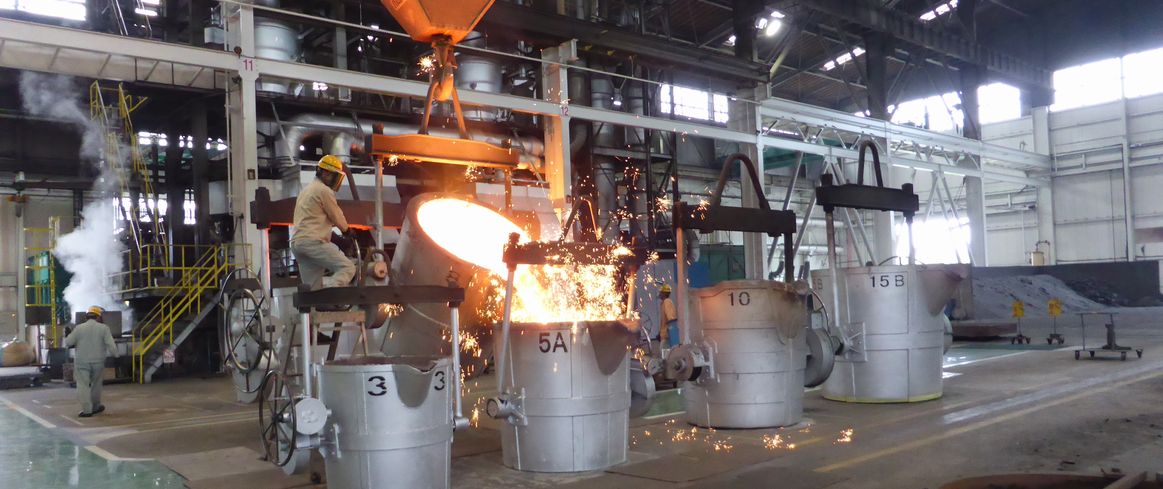
The Tanda Foundry Shop has been operation since October 1992
The foundry shop building is 9,894 ㎡10t/h Cupola (Hot-blast Water-cooled): 2 |
30t/15t/h Paramount Mixer: 2,etc. 4 |
Oscillating Mold-making System: 2 |
20-ton Sand mold dryer: 1, etc. 2 |
30-ton Shot-blast machine: 1 |
20-ton Shakeout machine: 1 |
10-ton Casting sand processing machine: 1 |
Casting sand cooling machine: 1 |
Emission spectrophotometric analyzer: 1 |
75 kW Compressor: 2, etc. 2 |
50-ton Crane: 1, etc. 19 |
Band saw, etc |
1-ton Crane: 1 |
Chiller-classifying Robot system : 1 |
2-ton Crane: 2 |
7.5 kW Compressor: 1 |
700kg Shot-blast machine: 1 |
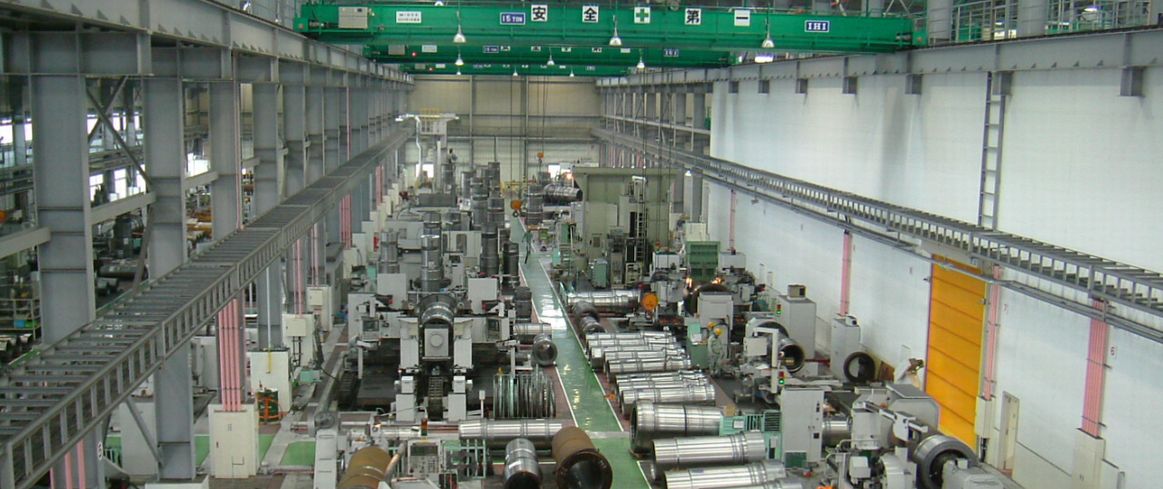
The Tanda Machining Shop (2 buildings) has been in operation since March 2005
No. 1 Machine, No. 2 Machine, No. 3 Integrated Factory8,639 ㎡(2,618 ㎡)
NC lathe: 10 |
Inside Boring Machine: 7 |
Machining center: 7 |
Cooling hole processor: 4 |
2-axis port processor: 4 |
Honing processor: 3 |
Other processing machine tools: 9 |
Other equipment: 25 |
15-ton Crane: 6, etc. 7 |
Heating Furnace 1 |
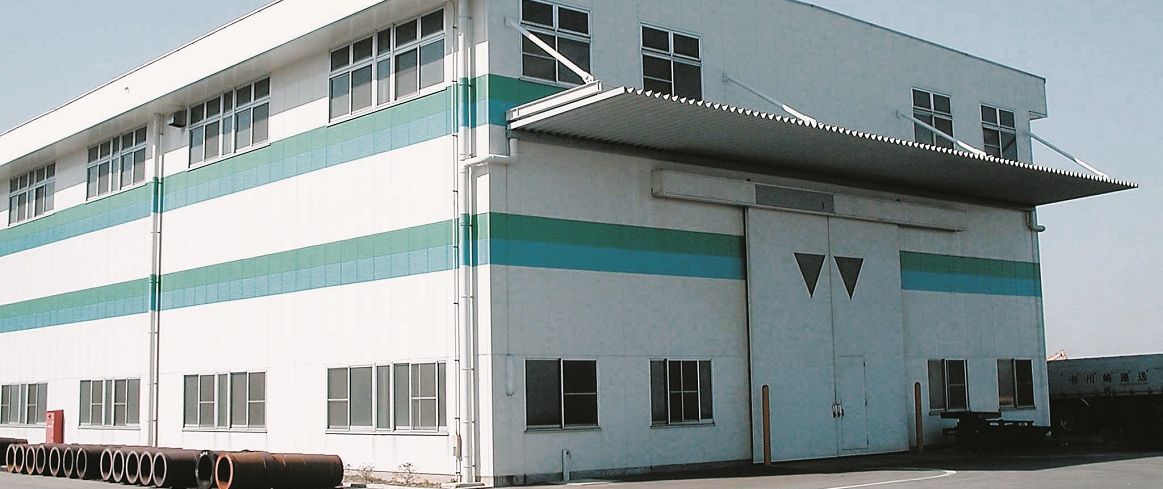
No. 4 Machine Shop
3,563 ㎡NC Lathe: 10 |
Inside Boring Machine: 7 |
Annealing furnace: 4 |
Other machinery: 12 |
20-ton Crane: 1, etc. 2 |
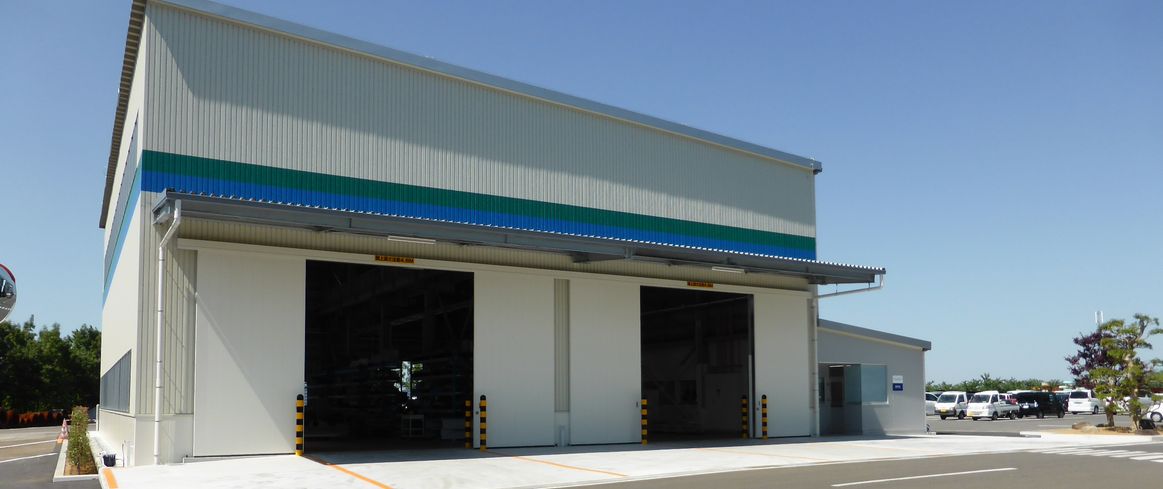
May 2018 Assembly shop started operations
rea of Assembly shop846㎡
15-ton crane: 2, Others: 2 |
Omuragata Factory
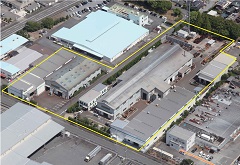
The Omuragata Factory has been in operation since May 1986
Site area: 29,448㎡In 1986 Riken Piston Ring Co., Ltd. ceased production of cylinder liners for medium-speed diesel engines. Taking on that business required a centrifugal casting production facility. Therefore, we constructed the Omuragata Factory at the Omuragata Industrial Park in Furueda, Kashima City. The new facility was also equipped with a ductile casting production system.
In 2005, we constructed a machine shop and added new equipment in order to improve our production capabilities so that we could meet the demand of our orders. This was done with the ultimate goal in mind of creating a comprehensive production system that included the entire process from basic materials to machine finishing and shipment in a single factory.
Currently we have all the equipment required for processing materials, completing, and inspecting not only cylinder liners but also cylinder covers. We therefore have achieved our goal of creating a production environment that can handle customers’ orders.
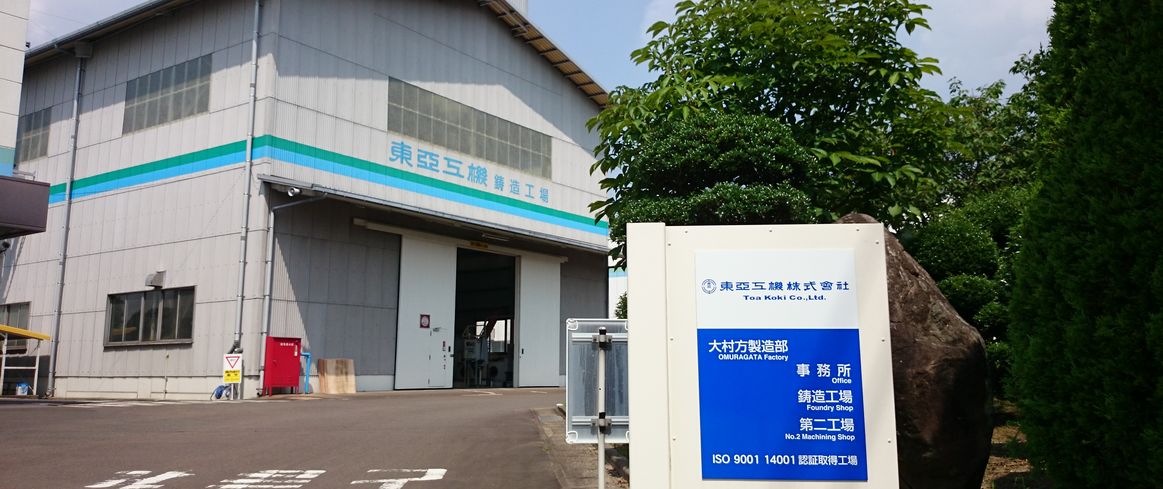
2,535 ㎡
3-ton Medium-frequency Induction Melting Furnace: 1 |
1-ton Medium-frequency Induction Melting Furnace: 1 |
SAVEWAY System 1 |
20-ton casting sand kneading equipment: 1, etc. 2 |
Oscillating Mold-making System: 2 |
Centrifugal casting machine: 3 |
2.8-ton monorail shot blasting machine: 1 |
7-ton shakeout machine: 1 |
5-ton casting sand reclaimer: 1 |
Sand cooler: 1 |
Annealing furnace: 2 |
Optial Emission Spectrometer: 1 |
10-ton crane: 3, etc. 9 |
37kW Compressor: 1 |

Building 1: 1,054 ㎡
NC lathe: 5 |
Inside Boring Machine: 3 |
Turning machine: 3 |
Other machines: 1 |
10-ton crane: 1, etc. 3 |
Building 2: 1,143 ㎡
NC lathe: 4 |
Inside Boring Machine: 3 |
Gun drill: 3 |
Machining center: 2 |
Other machines: 7 |
5-ton crane: 3, etc. 3 |
3D-Coordinate Measuring Machine: 1 |
22kW Compressor:1 |
Building 3: 1,086 ㎡
Turning center: 1 |
Turning machine: 2 |
Machining center: 2 |
Radial drilling machine: 2 |
5-ton crane: 2, etc. 3 |
3D coordinate measuring machine: 1 |
22kW Compressor:1 |
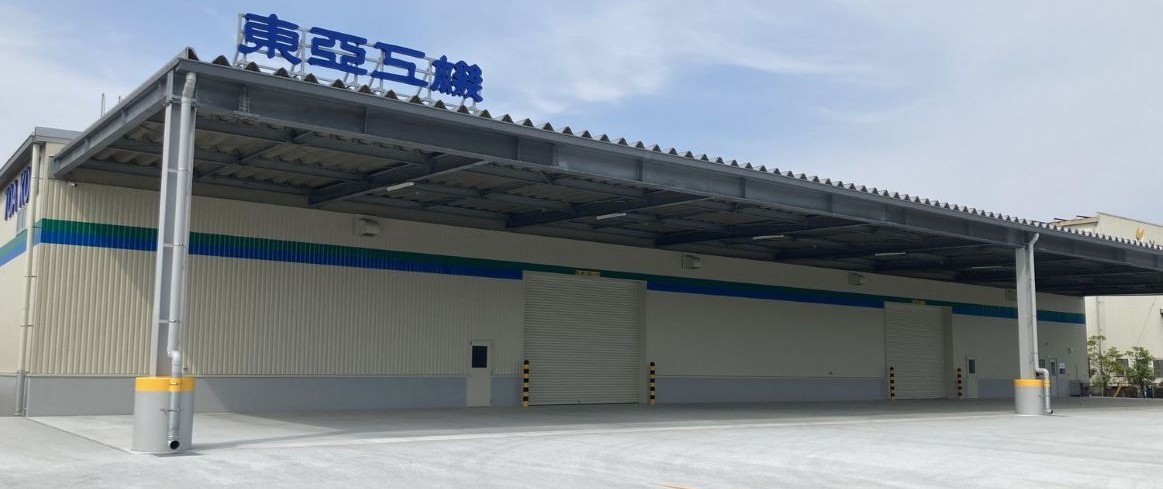
site area 5,067㎡ / building area 2,948㎡
Yokota Factory
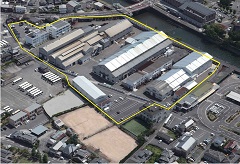
The Yokota Factory began operations in June 1944 and resumed operations in September 2008
Site area: 25,231 ㎡After the foundry and Machining department at the Yokota Factory, the company’s original site, were consolidated and transferred to the Tanda Factory in 2004, the Yokota site ceased operations. But in September 2008 production there was resumed.
As part of our factoryo diversity production at the Yokota Factory, in December 2014 a 3-ton intermediate frequency furnace that uses the electric power source of the 8-ton furnace already at the factory was newly installed. This allowed us to restart the factory as a production center for small- to medium-sized cast components.
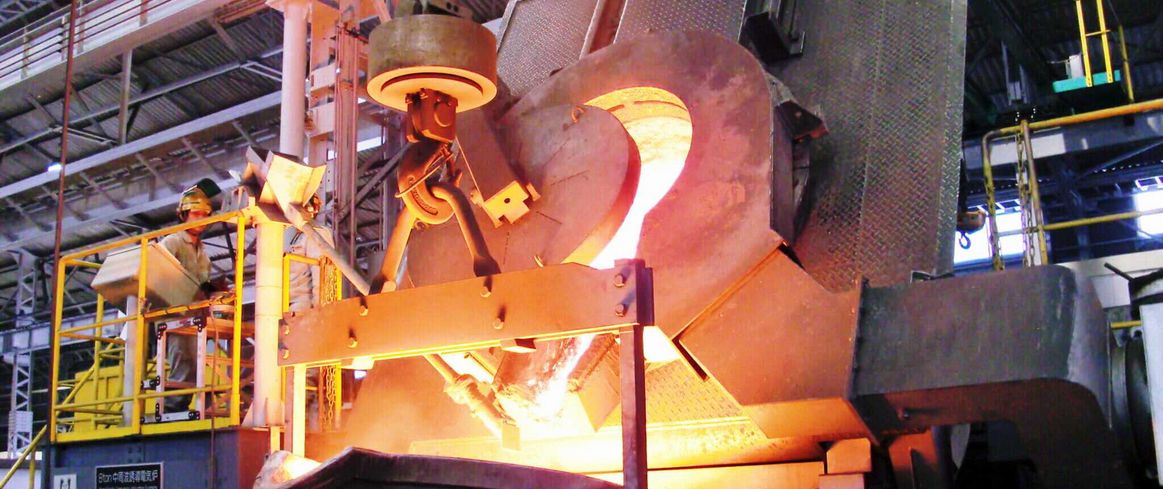
8-ton Medium-frequency Induction Melting Furnace: 1 |
3-ton Medium-frequency Induction Melting Furnace: 1 |
SAVEWAY System: 1 |
20-ton casting sand kneading machine: 1, etc. 2 |
Centrifugal Casting Machine: 1 |
15-ton monorail shot blasting machine: 1 |
10-ton shakeout machine: 1 |
10-ton casting sand processing machine: 1 |
Casting sand cooler: 2 |
Optial Emission Spectrometer: 2 |
Annealing Furnace: 1 |
30-ton crane: 1, etc. 17 |
37kW Compressor: 1 |
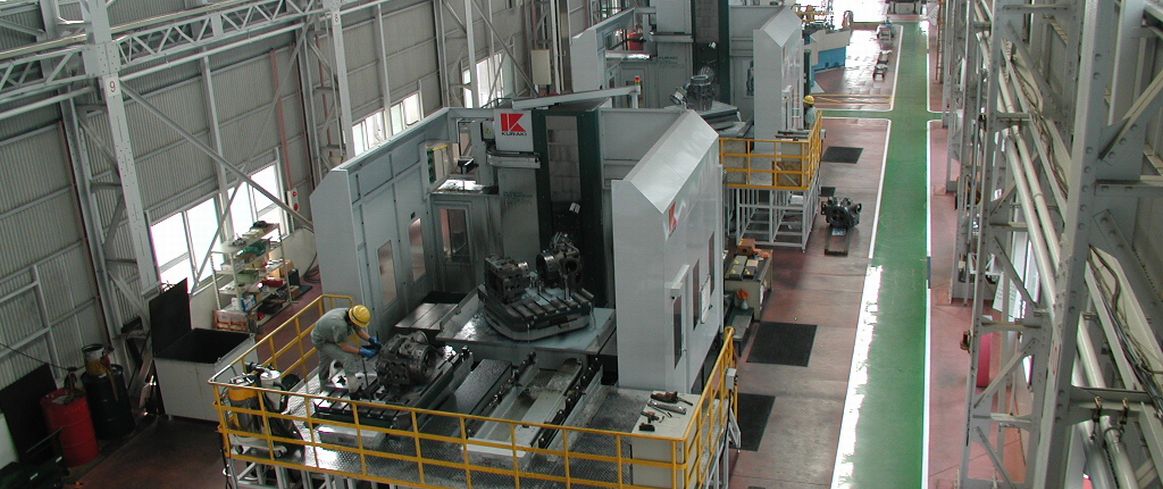
Building 1:548㎡
Machining center:1 |
2.8-ton crane:2 |
NC turning machine: 2 |
Machining center: 2 |
Other machines: 4 |
7.5-ton crane: 1, etc. 2 |
NC lathe: 5 |
Inside Boring Machine: 4 |
Machining center: 1 |
Horning processor: 2 |
Other machines: 3 |
15-ton crane: 1, etc. 9 |
Annealing furnace: 1 |
3D coordinate measuring machine: 1 |
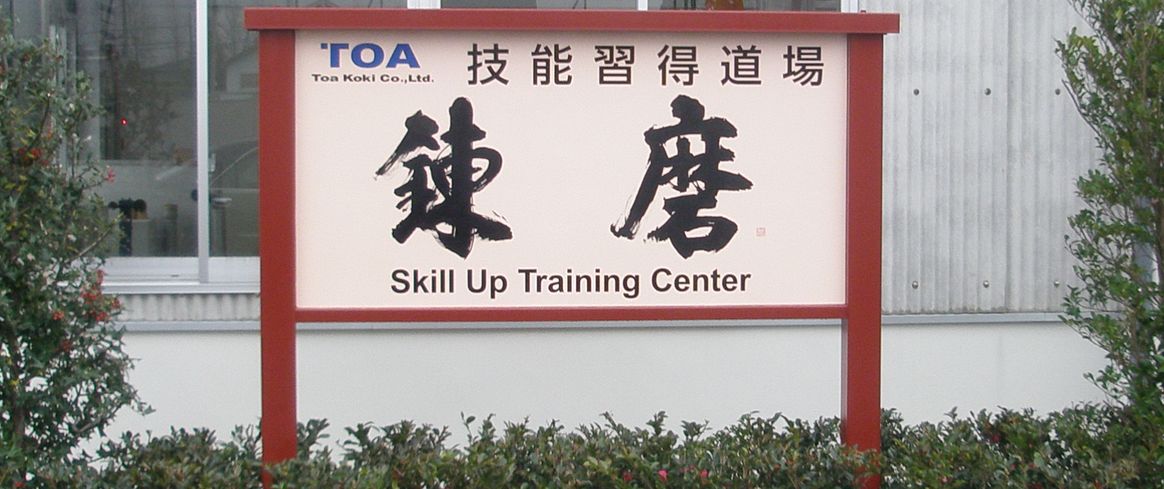
- Passing on Skills and Technology -
The “Renma” Center was established in order to pass on highly-advanced individual skills and techniques required by highly-advanced numerical control Machining as this type of processing becomes increasingly automated.
At the “Renma” Center, employees not only learn by observing veteran employees demonstrate their skills and techniques, they also learn the basic techniques of casting, processing, and finishing from these veterans and participate in an aggressive educational system in which they master these skills through hands-on training.
![]() |
1.Casting |
![]() |
2.Machining |
![]() |
3.Hand finishing |
![]() |
4.Finished work |
Research and Development FacilityR & D equipment
aterial quality
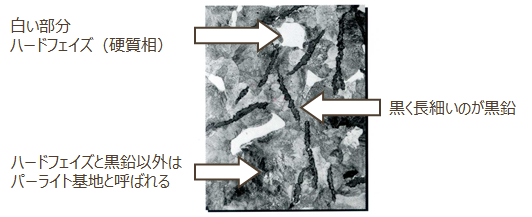
TARKALLOY® for use in large liners (100x magnification)
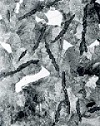
TARKALLOY® product matrix cast using the stationary casting method
The structure is layered with graphite flakes on a pearlite base matrix with hard phase distributed evenly throughout. It is used in the manufacture of cylinder liners ranging in size from small to large.
In any product, the graphite and hard phase must be evenly distributed within the pearlite base matrix. The hard phase improves wear and abrasion resistance and the graphite improves lubricity. The strength, elasticity, hardness, and chemical composition of these structures must meet standards.
Special cast iron for use in centrifugal cast cylinder liners (magnified 200x)
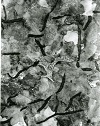
Since these products are manufactured using centrifugal casting, the graphite and hard phase layers are small and dense within the pearlite base matrix, which produces a high degree of strength. This method is used in the manufacture of small and medium-sized cylinder liners.
Ductile cast iron ferrite base matrix (magnified 100x)
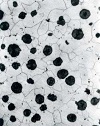
Since the graphite contained in Ductile is round, it is known as “spheroidal graphite cast iron.” Toa Koki’s spheroidal graphite cast iron is used in many products, including ship components and cylinder covers for generators.
R&D and testing equipment
The microscopes shown below are used to determine the numerical data we require in order to provide customers with the material quality they demand.
Since inspections have become more strict over the years, we need to use these instruments to conduct detailed checks of the numerical values of our products.
Leica microscope
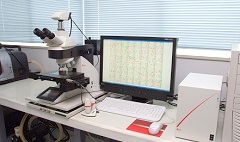
Mainly, we determine the size (length) of the graphite and the amount of hard phase. The instruments are able to automatically measure a specific area. When we receive a new order, we use these instruments to check the product specifications.
Digital microscope + Super depth multiple angle lens
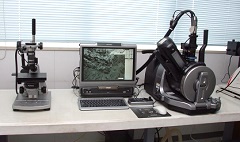
the amount of hard phase, and therefore they are one of the most commonly used instruments at Toa Koki.
Other test equipment
System inverted metallographic microscope3-D CAD and computer simulation system
Oil-hydraulic Brinell hardness tester
Electric muffle furnace
Sand tester
Surface roughness tester
Ultrasonic investigation equipment
Dynamic and fatigue test system
Introduction to the Technical Services Division and Environment Health Safety and Quality Assurance Department
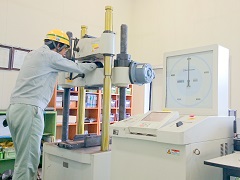
Testing Bureau, Inspection Division, Environment, Health, Safety and Quality Assurance Department
The universal testing machine is a testing device that measures products’ strength and elasticity. A sample of each product is always tested. Since the test pieces are stressed until they break apart, the testing room is usually very noisy.
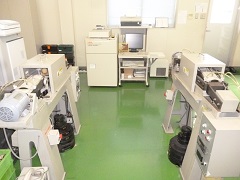
Research & Development Department, Technical Services Division
We are conducting research into how to manufacture stronger cylinder liners with increased wear-resistance. In March 2008, we added a rotary bending fatigue testing machine and in March 2010 we added an optical x-ray analyzer to the testing department in order to allow us to conduct higher quality research.
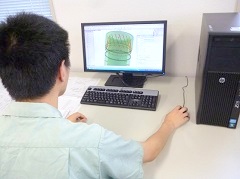
Design Department, Technical Services Division
Technicians in the Design Department mainly create versions of customer drawings that are used for in-house production. Currently, these drawings are efficiently produced using computers.
Technical Skill Certification HoldersQualified person
Minister of Health, Labour and Welfare Prize
Contemporary Master Craftsmen (outstanding technicians)
November, 2015 Hidemi Tahara [Machining]November, 2015 Masatoshi Ichinose [Pattern]
November, 2020 Masanori Fuchikami [Casting]
※About the Contemporary Master Craftsmen (outstanding technicians) Prize
Japan Vocational Ability Development Association certification: Highly-skilled workers
Machining (transportation machinery and equipment manufacture):1Ministry of Health, Labour and Welfare, Monodzukuri Master
Casting:4Machining:2
※Information about Monodzukuri Masters
Japan Ship Machinery & Equipment Association, Ship Master Certification
Casting:4Machining:3
Designing:1
Finishing:1
※Information about Ship Masters
Saga Master:1
※Information about Saga MastersToa Koki’s “Master & Associate Master” system
Masters:3Associate Masters:3
Technical Skill Certification Holders
Special Class Casting Technicians:5Special Class Machining Technicians:4
Special Class Finishing Technicians:2
First Class Casting Technicians:61
First Class Machine Technicians
General lathe:23Milling machine Technicians:6
Machining Center Technicians:13
First Class Finishing Technicians
Tool Finishing Technicians:6Machine assembly finishing:3
Mold finising:1